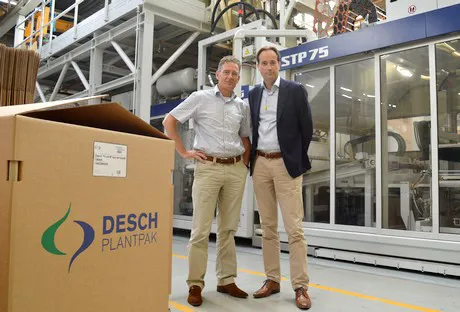
Wouter Zieck and Jan Willem Wieringa in front of their Thermoform container machine. (Next to thermoform, they also produce injection moulded pot, container and trays.)
Recycled plastic
Nowadays, people are more concerned about the environment. In general, plastic has a less positive image. However, when it is being recycled, the impact on the environment is a lot less, but people are not always aware of that. So, even though Desch Plantpak was always using as much recycled plastic as possible for their trays, pots and containers, they recently decided to put this activity in the spotlight. "Most of our injection moulded and thermoform trays, containers and pots consist of up to 100 percent recycled plastic. And as Wieringa mentioned, people need to be educated to recycle their plastic products", says Wouter Zieck, Director Sales & Marketing at Desch Plantpak who's been working at the company for 25 years. In order to educate people, the company made a short and clear video that explains how Desch Plantpak recycles plastic and how the end user can give this product a new 'future' by just putting it in a recycling bin.
Degradable product
However, if you cannot educate the people, you may offer them a new solution. And this is what Desch Plantpak decided to do in 1996 when they started to trial different kinds of biodegradable products. "We were looking for a non-oil-based inert product that would not affect the growth of the plant. After years of designing and testing, we were able to put the first biobased / biodegradable pots on the market in 2010 and we named it the D-Grade®", says Zieck.
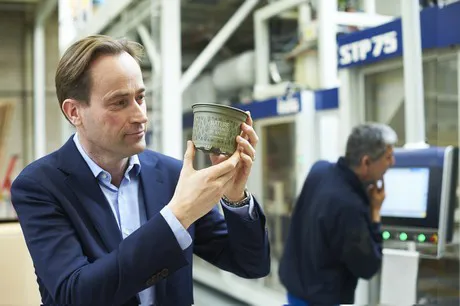
Wieringa holding a D-Grade® pot. (Photo taken by Kees Waqué)
The product has been on the market for several years now, but how is the demand developing for this product? "We see a growing interest in this product, but price-wise it's still an expensive product for many growers. Only the material is about three times as expensive as that of a regular pot. However there are applications when looking at the total costs including disposal, it actually becomes cheaper", says Wieringa.
Trendsetter
According to Zieck, with this non-oil based D-grade, Desch not only put a new product on the market, they also set a trend. "Before we introduced the D-grade, there were several biodegradable containers on the market, but none that were 100% free of oil components", says Zieck. And setting a trend seems to be in the company's DNA. In the late 1980s they, explains Zieck, were the first plastic container manufacturer that decided to manufacture thermoform pots for the horticulture sector.
Thermoform
Thermoform enables Desch to use less plastic for a pot, container or tray, but manufacturing thermoform products for the horticulture industry is not as easy as it sounds. "The machine itself is a very expensive investment. Therefore, only a handful of horticultural packaging manufacturers have one. Besides that, the thin walls, that result in a favorable price for growers, used to transmit light which affect the growth of the roots. Therefore, we've adjusted the composition of the plastic. Now, it does not transmit any light, leads to improved root growth", says Zieck.
At the location in Waalwijk, the Netherlands, Desch Plantpak, produces these thermoform trays and containers. Below an impression of the process of how these trays and containers are produced.
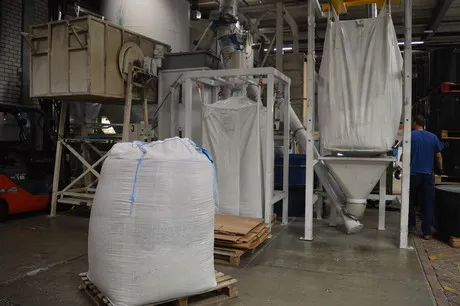
Big bags of recycled plastic on the left and on the right a big bag being emptied. The plastic will be blended to the right specifications.
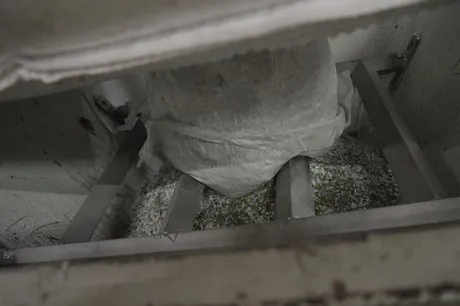
The recycled plastic.
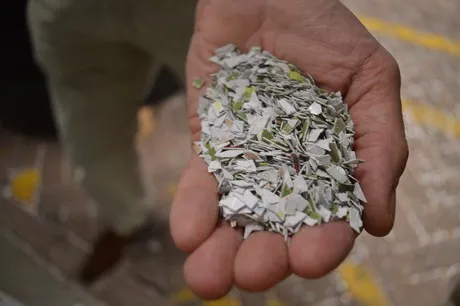
Zieck gives us a close up of the plastic. It contains all kinds of plastic material, like food packaging, used trays from growers, coat hangers, and even fridges.
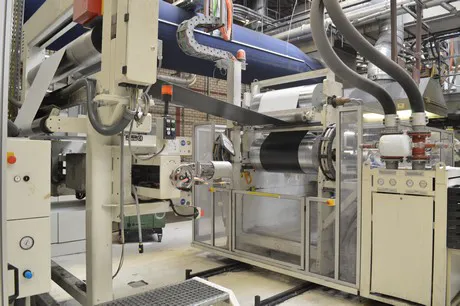
The black and white film.
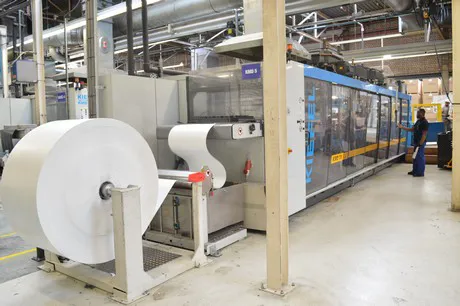
In this area, the trays are produced. Currently, the Normpack 400 tray is being manufactured. According to Zieck, Desch Plantpak is one of the few licensed manufacturers for Royal FloraHolland to manufacture these trays.
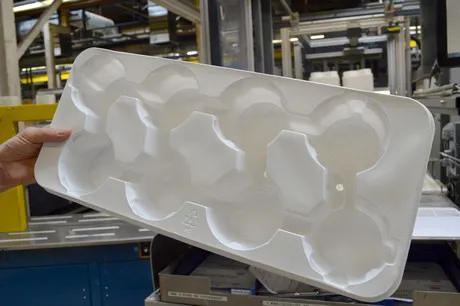
The end result; the Normpack 400 tray.
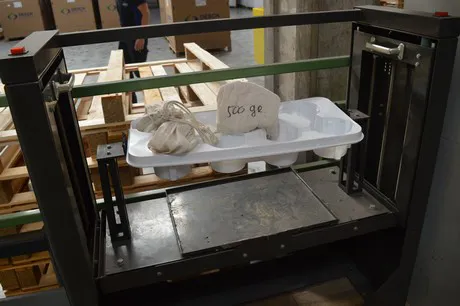
The trays, this Normpack tray for example, needs to carry an amount of weight when holding it with two hands or one hand without bending through.
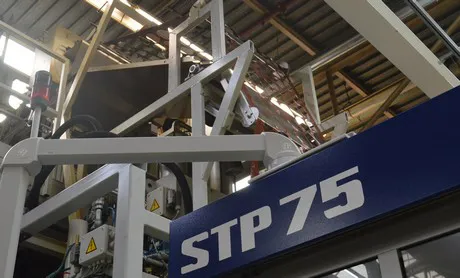
The waste plastic is directly discharged and collected.
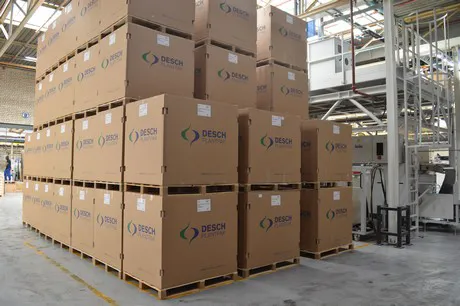
Desch Plantpacks pots ready to leave the factory.
Colour Your Story
Another way how Desch Plantpak is aiming to set trends is by inspiring growers and retailers with pot-plant combinations. "In September a new booklet will be available. In this 48-page book, all kinds of combinations with several pots and containers will be displayed, with special attention given to the FleuroStar winner and FleuroSelect Gold winners", say Kees Waqué, Manager Retail & Marketing at Desch Plantpak.
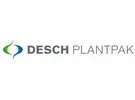
Desch Plantpak B.V.
Email: [email protected]
www.desch.nl